Our client had recently built his retirement home in the San Juan Islands. The spray foam that was installed was improperly mixed, and caused significant VOC off-gassing concerns. The home had been inundated with flies, and the client hired Hawk Environmental to assess these issues and generate a plan for resolution. The following information includes excerpts from the final report and shoes how the concerns can be investigated.
Background information:
The home has been under the final stages of construction, and the client has had the following concerns:
- Poorly mixed 2-part polyisocyanurate insulation was installed. The failed portions of insulation were removed and replaced by the contractor prior to the inspection.
- An infiltration of a large quantity of flies into the home.
Based on the concerns above the client has requested the following services:
- VOC testing to determine if excessive off-gassing is present due too the insulation.
- Blower door testing with infra-red evaluation to determine if portions of insulation are missing and if gaps are present which may allow the flies to enter into the living space.
Property description:
The subject property is a 3,200 square foot single-family home that is in the final stages of construction, but is currently occupied.
LIVING SPACE VENTILATION
Current conditions:
The living space in the home is currently ventilated by:
2 LifeBreath 155ECM HRV systems. Each system is connected to an air-handler and air conditioning unit located on the second level of the home.
The HRV’s are installed in a “partially dedicated” configuration (i.e. the HRV fresh-air supply connects directly to the air handler return duct, and the stale-air intakes draw directly from the home). *The majority of the ducting for these systems is located within inaccessible ceiling cavities and no duct-design plans were provided.
The HRV’s do not appear to be interlocked to the air handlers as is recommended by the manufacturer. This condition may limit the ability for fresh-air to be distributed throughout the home.
Excerpt from LifeBreath 155ECM manual: “It is recommended that the furnace blower run continuously, or HRV operations be interlocked with the furnace blower to evenly distribute the fresh air throughout the house.”
The HRV’s are controlled by two TI-DXPL-01 controllers (mounted in the master bathroom and guest bathroom)
No manual dampers were found on the main HRV ducting, and it is assumed that the contractor attempted to balance the systems through the adjustable register vents.
The exhaust fans and registers in the home were tested with an Alnor 6200 balometer and the following flows were recorded:
Mechanical Room/ Crawlspace: 70 CFM
Basement Laundry Room: 46 CFM
Basement Toilet: 67 CFM
Guest Bathroom Toilet: 22.5 CFM
Guest Bathroom Shower: 26 CFM
Main Laundry: 23 CFM
½ Bathroom: 24.6 CFM
Master Bathroom Toilet: 30 CFM
Master Tub Area: 19 CFM
Steam Shower: 64.6 CFM
Master Closet: 16 CFM
Master Bedroom: 24 CFM
The home is also equipped with a large exhaust fan that empties into the crawlspace, this fan draws from a register on the ceiling above the loft, but does not have any damper to prevent the loss of warm air.
Insufficient ventilation in the living space of the home can lead to a buildup of humidity (contributing to mold growth in the living space and attic space), a buildup of miscellaneous building pollutants (such as VOC’s from cleaners, fragrances, cosmetics, and building materials), and is significant contributing factor to a wide range of indoor air quality concerns.
Environmental Data:
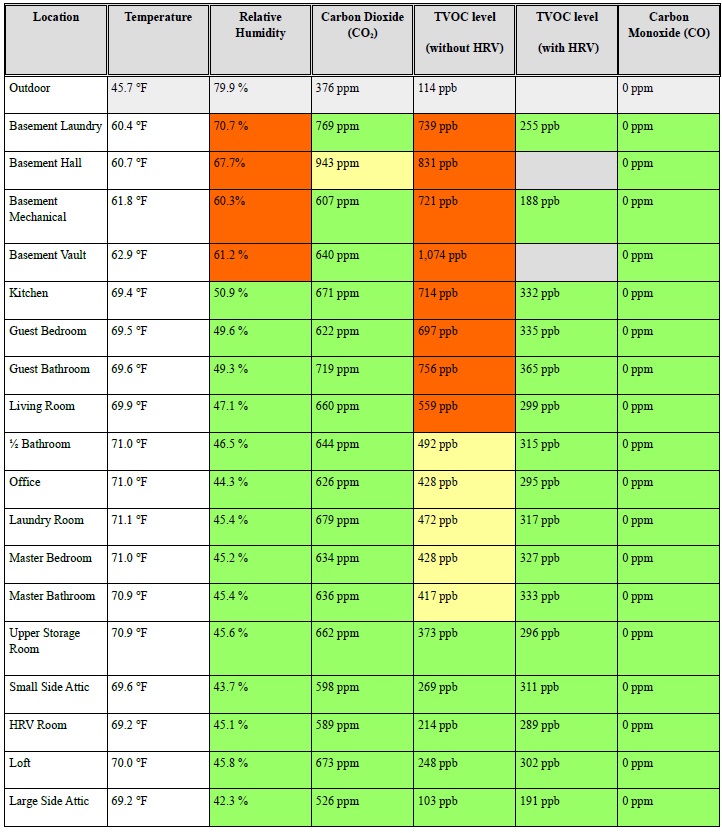
Evaluation:
- Temperature: The temperature in the living space is fairly consistent throughout the home, and should not have a negative impact on indoor air quality.
- Humidity: The humidity levels in the majority of the home was within recommended limits, and the areas outside of the range were limited to the lower level and likely reflect outdoor air rather than typical indoor conditions.
- Carbon Dioxide: The carbon dioxide levels in the home were mostly within the recommended levels, but this is likely due to the few number of occupants per square foot in the home.
- Total VOC’s (volatile organic compounds): The tVOC levels in the home were at or above the recommended limits, but can likely be reduced significantly with improved ventilation (i.e. interlocking the HRV’s to the air handler and running them more frequently).
- Carbon Monoxide: No carbon monoxide was detected at the time of inspection.
Recommended Ventilation Rates:
As per 2013 ASHRAE 62.2 (these requirements are in excess of Washington State’s most current building codes, but Hawk Environmental Services prefers a more liberal ventilation plan)
Floor Area in Ft2 | Number of Bedrooms | ||||
---|---|---|---|---|---|
1 | 2 | 3 | 4 | 5 | |
<500 | 30 | 38 | 45 | 53 | 60 |
501-1000 | 45 | 53 | 60 | 68 | 75 |
1001-1500 | 60 | 68 | 75 | 83 | 90 |
1501-2000 | 75 | 83 | 90 | 98 | 105 |
2501-3000 | 105 | 113 | 120 | 128 | 13 |
3001-3500 | 120 | 128 | 135 | 143 | 150 |
3501-4000 | 135 | 143 | 150 | 1558 | 165 |
4001-4500 | 150 | 158 | 165 | 173 | 180 |
4501-5000 | 165 | 173 | 180 | 188 | 195 |
Inspection Observations (general):
Significant air leakage was found on infrared inspection at the tops of each dormer, above the kitchen windows, and at the top of the rear knee-wall in the large attic (see pictures below):
Insects (Flies):
- The client has been experiencing a large amount of flies entering and becoming trapped in the home.
- The dead flies were visually evaluated and are consistent with “cluster flies”
- The cluster flies are the genus Pollenia in the blowfly family Calliphoridae. Unlike more familiar blow flies, such as the bluebottle genus Phormia, they do not present a health hazard because they do not lay eggs in human food. They are strictly parasitic on earthworms; the females lay their eggs near earthworm burrows, and the larvae then infest the worms. However, the flies are a nuisance; when the adults emerge in the late summer or autumn, they enter houses to hibernate, often in large numbers; they are difficult to eradicate because they favour inaccessible spaces such as roof and wall cavities. They are often seen on windows of little-used rooms. They are also sometimes known as attic flies. Pollenia sp. on leaves in a forest. The typical cluster fly Pollenia rudis is about 7 mm long and can be recognised by distinct lines or stripes behind the head, short golden-coloured hairs on the thorax, and irregular light and dark gray areas on the abdomen. Cluster flies are typically slow-moving. Cluster flies have a widespread distribution. Eight species are found in Britain and 31 in Europe. Pollenia species are also numerous in Australia and New Zealand (over 30 species); they are a common pest in North America. P. rudis has spread widely in association with humans.
- Dead flies were seen on fly-strips, window sills, and within the HRV units.
- The flies appear to be entering the home from gaps at the dormer eaves, where then can migrate through the coffered ceiling space and throughout the home.
- While the home was being depressurized with the blower door the inspector used the client’s lift to access the eaves above the living room windows. At the eaves flies were seen entering through gaps around the tongue-and-groove soffit. These gaps were then tested with a small smoke generator and a large amount of air infiltration was observed. It is assumed that the flies are entering the coffered ceiling from gaps at the dormers and then migrating throughout the home.
- Additional areas of insect infiltration may exist, but could not be determined at the time of inspection.
Blower Door Testing
The air leakage in the home was tested with a Minneapolis Blower Door, DG-700 manometer, and the Energy Conservatory’s Tec-Tite software. All tests were performed with the HRV units deactivated, all windows and doors closed, and the blower door installed in the lower level exterior door.
The detailed reports are included in separate pdf documents but the results are as follows:
2012 Washington State Energy code requires the ACH 50 of 5.0 or less.
Doors to attics closed and “heat-dump” register sealed with plastic:
2,793 CFM @ -50 pascals = 4.94 ACH 50
Doors to attics closed and “heat-dump” register open:
3,053 CFM @ -50 pascals = 5.07 ACH 50
Doors to attics open and “heat-dump” register open:
3,195 CFM @ -50 pascals = 5.31 ACH 50
Recommendations:
Ventilation:
Re-wire the HRV units and controls to ensure that they will be interlocked to the air handlers as is recommended in the installation instructions.
Install appropriate in-line dampers on the main HRV ducts and tune and balance the system as per manufacturer’s instructions.
Once the system is properly connected and balanced, measure the total HRV flow and set the two systems as per the ventilation recommendations listed above (total of 128 CFM).
Once the HRV system is properly set up measure the flows from the exhaust registers in bathrooms and laundry room and ensure that they meet the minimum requirements for spot ventilation.
The spray-foam insulation does not appear to be releasing significant VOCs into the home, and is unlikely to negatively impact indoor air quality.
Flies:
Areas of infiltration should be sealed as much as possible.
Strip all tongue-and-groove soffits, underlying OSB, and seal all gaps between framing and/or sheathing with expandable foam sealant or caulking.
Strip all window trim and/or surrounding drywall at the dormers and seal all gaps between framing and/or sheathing with expandable foam sealant or caulking. This will also require creating access points to the coffered attic near the gable ends of the dormers and sealing those areas as well.
Air leakage:
Install a damper on the “heat-dump” ducting and vent the exhaust from that system completely to the exterior.
Sealing gaps at the dormers as listed above for insect exclusion will likely provide a significant decrease in air leakage.
Sealing any remaining electrical or plumbing penetrations in the crawlspace will likely provide some decrease in air leakage.
Stripping trim from around the kitchen windows (areas where space for electronic window coverings was installed) and sealing gaps in framing or sheet-rock with expandable foam sealant or caulking will likely provide some decrease in air leakage.
Removing the FSK barrier in the large attic may provide access to areas of missing insulation or air-sealing that is responsible for the air infiltration shown in the photos above.
Additional notes for future investigation or improvements:
The fresh-air intake ducts for the 2 HRV’s do not appear to be insulated as is recommended, some insulation may be present in the inaccessible attic space, but the fresh-air duct within the conditioned space should be insulated.
The 2 attic spaces are technically part of the conditioned building envelope, but are not being used as conditioned spaces. These areas should be ventilated in accordance with the remainder of the building and not sealed from the main body of the home.
The drilled holes in the HRV ducting may have been installed to ventilate the HRV room, but do not appear to have been installed in a practice consistent with good workmanship.
The area between the crawlspace and mechanical room should not be sealed, as the mechanical room should technically be considered part of the unconditioned crawlspace.
The “vault” in the basement is not currently ventilated and may become excessively humid, or may concentrate any odors or off-gassing from stored materials. The client should investigate systems that are commercially available for wine cellars, where managing humidity via air exchange to the exterior is utilized.
Comments are closed.